
Liquid Printed Products
MIT SELF-ASSEMBLY LAB + CHRISTOPHE GUBERAN
Presented by PATRICK PARRISH GALLERY
Supported by swissnexBoston
Patrick Parrish Gallery, in collaboration with MIT’s Self-Assembly Lab and Christophe Guberan, and made possible by swissnex Boston and Presence Switzerland presents a futuristic manufacturing facility based on rapid liquid printing, a breakthrough 3-D printing technology developed in collaboration with Steelcase, which can rapidly produce objects of almost any size or shape using a robot and a tank of gel. The space serves as a manufacturing facility in which a robot instantly prints tote bags and art objects inside a glass tank of translucent gel. After printing, each product is removed, cleaned, and put on display. Visitors are able to move around the tank to observe the robot at work, and the produced items are for sale inside the booth. This exhibit is the first public demonstration of MIT’s rapid liquid printing technology. Rapid liquid printing can produce large-scale objects out of high-grade materials like rubber, foam, or plastic in a matter of seconds or minutes by “drawing” them in a gel suspension. Traditional 3-D printing is restricted by slow speeds, scale constraints, and poor material quality, which makes it unreliable as a mainstream manufacturing process. With rapid liquid printing, manufacturing can be reimagined as an artistic experience unlimited by scale or gravity, asking us to rethink design, production, uniformity, and product life-cycles.
Self-Assembly Lab Team: Bjorn Sparrman, Kate Hajash, Shokofeh Darbari, Schendy Kernizan, Jared Laucks & Skylar Tibbits
Liquid Printed Light
MIT SELF-ASSEMBLY LAB + CHRISTOPHE GUBERAN + MARCELO COELHO
In collaboration with STEELCASE Inc.
Presented by PATRICK PARRISH GALLERY
MIT’s Self-Assembly Lab, Christophe Guberan, Marcelo Coelho and Steelcase Inc. present a stretchable light created with Rapid Liquid Printing, a breakthrough 3-D printing technology which can rapidly produce objects of almost any size or shape using a robot and a tank of gel. The skin of the light was printed within an 18” cubic tank, suspended within the gel, then removed and washed with water. The printed silicon rubber, a material that would be nearly impossible to produce with any other printing technology, allows the skin to be stretched around a light tube or any other structure, making an object that is far larger than its original print volume. The stretchability of the material minimizes the size and duration of printing while also creating a minimal storage/shipping volume. This unique light skin can be customized to create different sizes or geometries by simply stretching the skin around different internal frames.
Design Miami 2017 is the first public demonstration of MIT’s rapid liquid printing technology. This process can produce large-scale objects out of high-grade materials like rubber, foam, or plastic in a matter of minutes by “drawing” them in a gel suspension. Traditional 3-D printing is restricted by slow speeds, scale constraints, and poor material quality, which makes it unreliable as a mainstream manufacturing process. With rapid liquid printing, manufacturing can be reimagined as an artistic experience unlimited by scale or gravity, asking us to rethink design, production, uniformity, and product life-cycles.
Self-Assembly Lab Team: Kate Hajash, Bjorn Sparrman, Shokofeh Darbari, Schendy Kernizan, Jared Laucks & Skylar Tibbits
Steelcase Team: Markus McKenna, Sharon Tracy, Paul Noll, Ed Vanderbilt, Charlie Forslund, Rob Poel






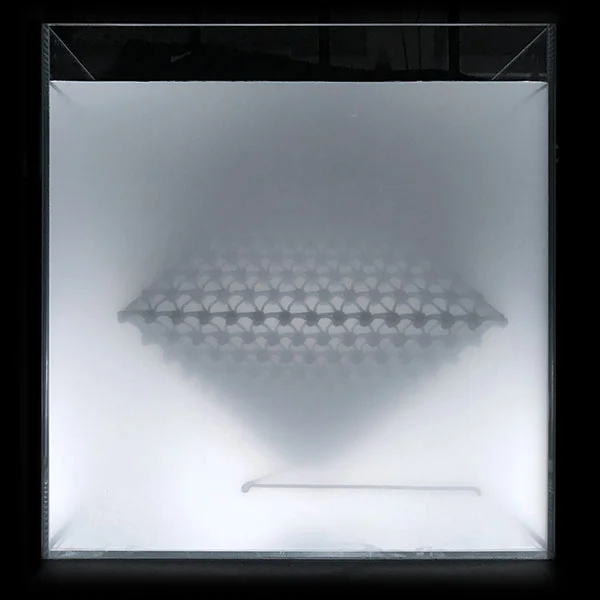



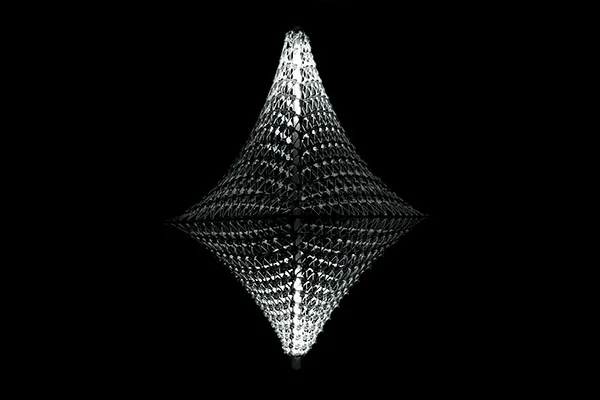

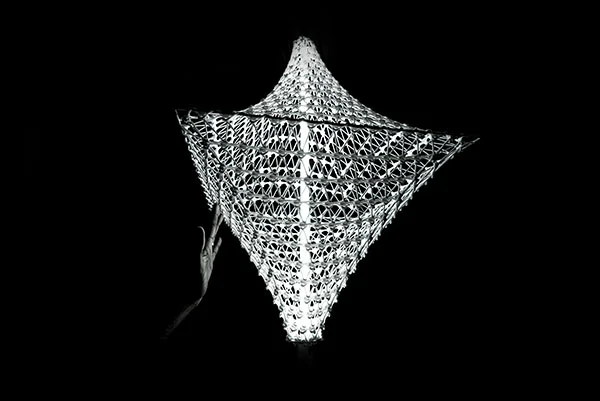


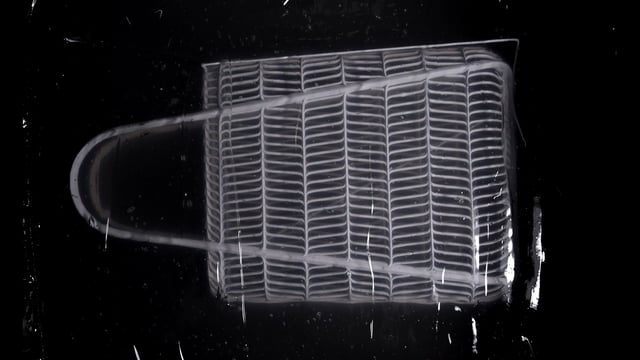
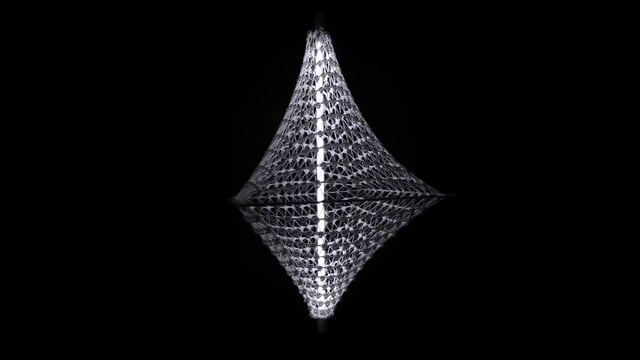






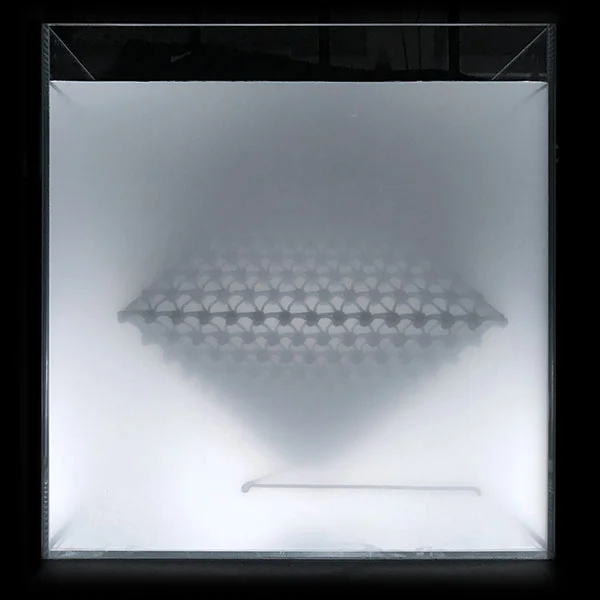



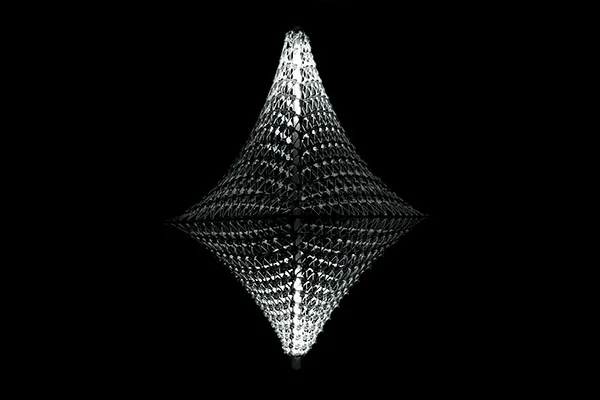

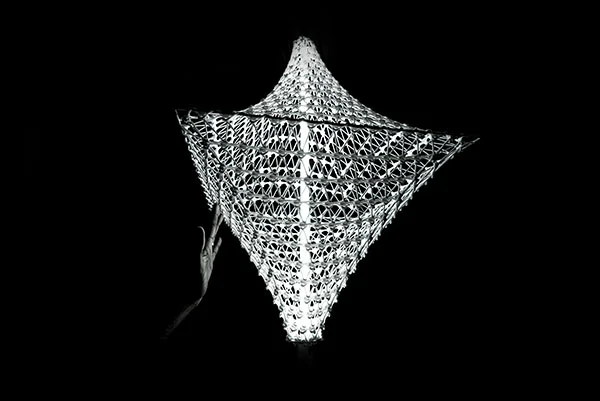


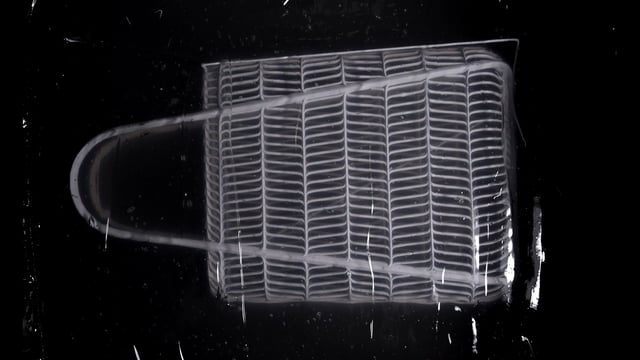
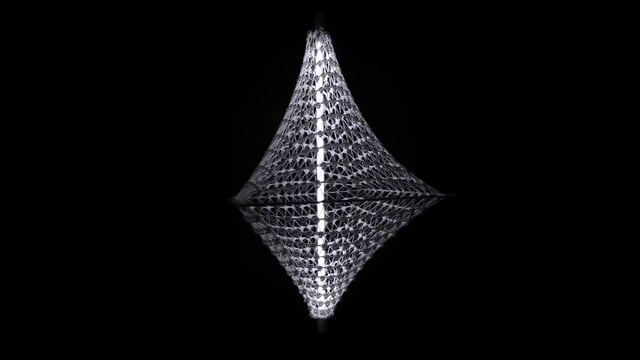